A metal finish is a manufactured decorative or protective coating like paint, enamel, powder-coating, and anodizing that’s applied to the surface of the metal. The process for applying a metal finish may vary depending on the desired effect.
Metal finishes can help give metals surfaces new textures and colors or make them more resistant to all sorts of wear Are you wondering to decide which finish to use on your metal components? So, this article is for you as it will discuss 60 different types of metal finishes.
[toc]
60 Types Of Metal Finishes That You Might Not Know
There are many ways to take a plain metal surface and make it into something beautiful. One way is to take that metal and apply a finish layer of paint or another coating. This can be done by hand with brushes, spray cans, or any number of equipment used for painting cars, furniture, etc. Another method is vacuum metallization. This is a process of spraying the metal with a solution that coats it with a thin layer of aluminum or other metal by removing the air in between, effectively vaporizing it.
1. Painted Metal Finishes
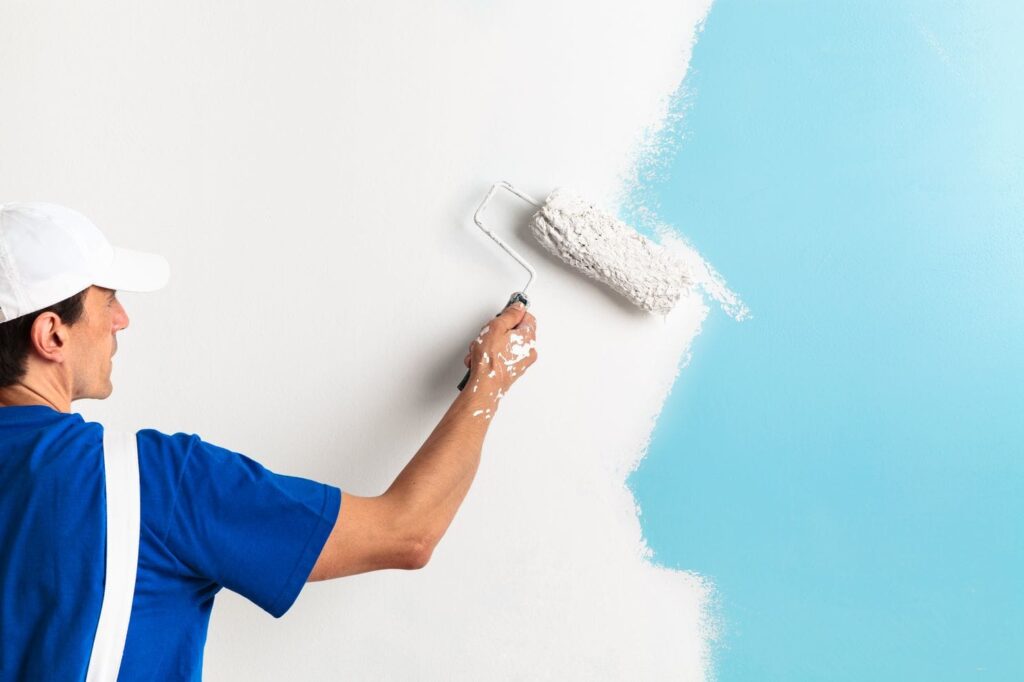
A painted metal finish is an effect achieved by painting a substrate with metallic paint, typically using a brush. As a result of the porosity of paint films, there is a surface enrichment on the part due to filling.
The difference between cold-rolled and hot-dipped galvanized parts, for example, is obvious after painting, as painted on a cold-rolled part will wipe off easily while a painted one remains intact on a galvanized substrate.
Examples
Some examples of painted metal finishes are powder coating, spray painting, and roller painting.
2. Powder Coating Metal Finishes
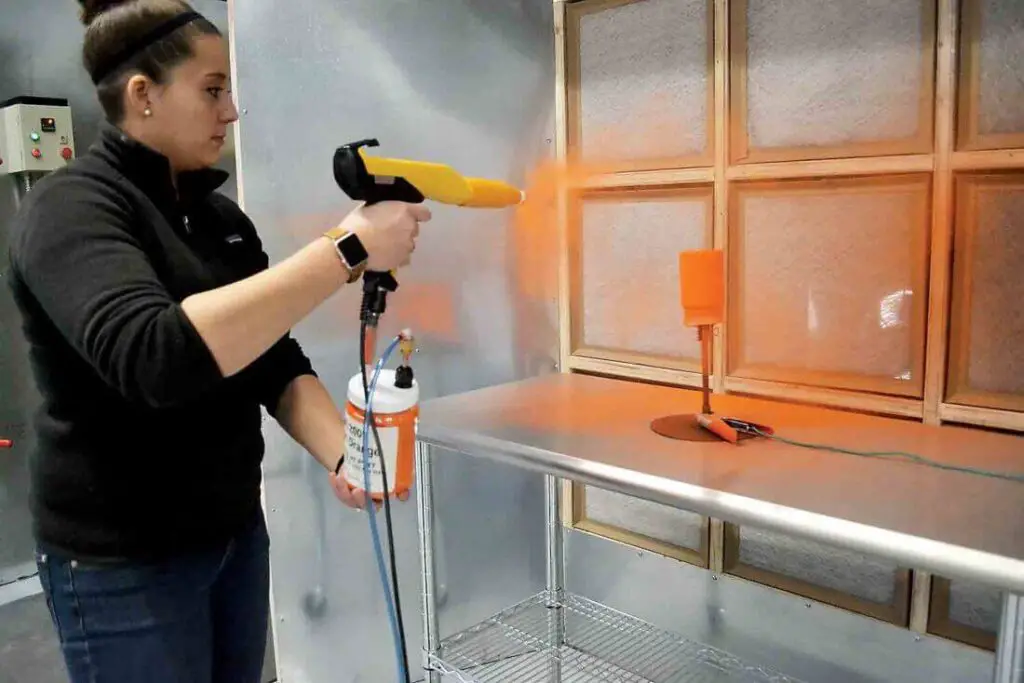
A powder pattern is a color effect achieved by mixing or applying dry colored pigments to a substrate, which can be flat or 3D. A special type of powder coatings is called granulates. In contrast to the earlier film forming method, these powder coatings use a chemical binder to hold the pigment.
The powder coats can be applied as dry or pre-mixed colors to create a variety of effects from flat surfaces to 3D objects that can mask shapes and features on a substrate.
Examples
Some examples of powder coating metal finishes are electrostatic application, slush molding, fluidized bed, hot spray, rotary atomizing, air knife.
3. Spark Plating Metal Finishes
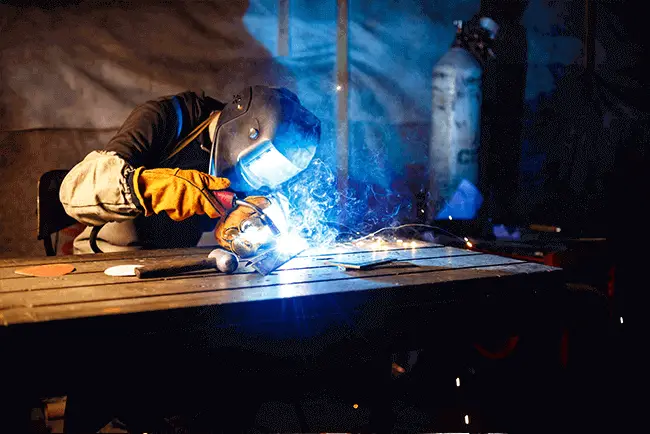
A spark plating metal finish can be used when a bright or mirror-like finish is desired on the workpiece. The result is different from that obtained in an electrolytic process and most cases, more attractive, with a brilliant luster.
The first step is to clean the workpiece with an alkaline cleaner. Then, it is rinsed and pickled before plating. A wide range of colors is available using this method, ranging from gold or copper colors to cobalt blue or black chromium oxide.
Examples
Some examples of spark plating metal finishes are chromic-acid, sulfuric acid, sulfate, cyanide.
4. Clear Anodizing Metal Finishes
A clear anodizing metal finish can be achieved by immersing the workpiece in a solution containing sulfuric acid at room temperature. The solution is absorbed into the workpiece by capillary action. The thickness of this film varies from 0.5 to 2 μm, depending on the power of the acid used.
When the immersion time and temperature are properly controlled, a good luster and good corrosion resistance can be obtained.
Examples
Anodizing metal finishes are used to provide an improved oxide film coating, which is corrosion-resistant. Anodized aluminum is for example commonly used as household appliances and can be dyed in a wide range of colors.
5. Vacuum Metallization Of Metal Finishes
A vacuum metallization metal finishes process is available to provide bright, highly reflective surfaces on most metals with a variety of colors. The basic vacuum metallization process has been in use for over 40 years and can be applied to most metallic surfaces that are free of contaminants or scratches. A spark plating finish is the final step done in this process.
Examples
Some examples of vacuum metallization metal finishes are vapor-deposited metals, spark plating, and chromic acid.
6. Silk Screening On Metals/Metal Substrates
A silkscreen printing process is used to selectively apply graphic images or text to most metals, plastics, and wood materials. A film of photopolymer is applied to the surface with an adhesive that can be removed later, after exposing it to ultraviolet light (UV-curable films), heat (thermal films), or solvent (solvent-based films). A dipping process can also be used instead of a film.
Examples
Some examples of silk screen printing on metals include donor boards for circuit boards, tagging parts and letters to make applications easier to identify or products easier to sort. Silk screening is also available in applications such as identification bracelets, product tags for items including cars, toys, sporting goods, appliances, and electronic devices.
7. Electroplating On Metals/Metal Substrates
An electrolytic process in which a metal or alloy is deposited on an article by applying an electrical current between the workpiece and a liquid metal electrode. A thin deposit of metallic material thus adheres to the article. The method of choice when a highly conductive, ductile deposit is desired.
Examples
Some examples of electroplating on metal substrates include the bright chrome finish found on automotive trim and accessories, such as grilles and light fixtures. Electroplated finishes also come in gold, silver, nickel, and tin-nickel alloy.
8. Hot-Dip Galvanizing Metal Finishes
A protective zinc coating, which provides corrosion resistance to metals. The process involves immersing the workpiece in molten zinc at a high temperature after pre-treating it with an alkaline cleaner.
Examples
Some examples of hot-dip galvanizing metal finishes include a corrosion protection process used to coat iron and steel. It is commonly used on chain-link fencing, guardrails, handrails, light posts, and other architectural structures.
9. Hot-Dip Aluminium Finishes
A process in which the aluminum is dipped into a bath of molten aluminum alloy or pure molten aluminum. The alloys vary in compositions and may be selected to create specific properties of luster, machinability, corrosion resistance, etc.
Examples
Some examples of hot-dip aluminum metal finishes include architectural, food service, beverage equipment, and beverage containers.
10. Electrophoretic Coating Metal Finishes
A process that uses electricity to transfer a fine particle powder onto the surface of a product. An anode is constantly charged, and particles constantly bombard the product. The powder sticks to the surface via a static electrical charge that forms as a result of friction between the product and powder.
Examples
Some examples of electrophoretic coatings include metal-plated products for the medical, pharmaceutical, electronic, and foodservice industries. The coatings can be clear or color, depending on the material used to create the powder particles. Color pigments are also available for specialty applications like transfers with barcodes and uniform identification numbers (USN).
11. Back Side Coloring On Printed Circuit Boards (PCBs)
A process that creates an image or text on the non-copper side of a PCB. It involves using a silkscreen, letterpress, and photographic processes to apply specially formulated inks to the non-copper side of a printed circuit board.
Examples
Some examples include serial numbers, identification labels, and circuitry designations.
12. Decorative Painting Metal Finishes
A process that paints decorative images on the surface of a metal. It is usually done after an item passes through a pre-treatment process that removes all oil, grease, and dirt from the surface.
Examples
Some examples of decorative painting metal finishes include ornamental iron, architectural steel, and appliances.
13. Chemical Polishing Of Metals
A polishing process that uses acid and abrasive chemicals to prepare a metal surface for further finishing processes. This is done to remove mill scale, rust, or other imperfections from the metal.
Examples
Some examples of chemical polishing include bright dipping, burnishing, and anodizing.
14. Solder Mask Coating On Printed Circuit Boards
A process in which the board is coated with a liquid photo-imageable solder resists material. It protects areas that do not need to be soldered from the process of applying solder paste and assembling components.
Examples
Some examples of solder mask coating on PCBs include prototyping and multi-layer boards.
15. Hot-Dip Tinning Metal Finishes
A process that coats steel with a very thin layer of tin, which provides rust protection or improves lubricity for ease of machining. It involves dipping the workpiece in a molten bath of about 270 degrees C and containing tin and lead.
Examples
Some examples of hot-dip tinning metal finishes include automotive parts, marine applications, and plumbing.
16. Acid Pickling Metal Finishes
A process that removes copper oxide and other impurities from stainless steel and carbon steel using an acid, such as nitric acid.
Examples
Some examples include passivation, non-chromic stripping, and chromic acid anodizing.
17. Brushing Metal Surfaces
A metal finishing process that uses a mechanical wire brush to move the surface of a metal in one direction. Brushing can be used to apply different finishes, depending on the angle at which the bristles are moved over the surface.
Examples
Some examples of brushing include parts with a satin or brushed finish, metal components that need to resist corrosion, and surfaces with an uneven finish.
18. Chrome Plating Metal Finishes
A process that produces a bright, wear-resistant, and corrosion-resistant finish by coating the product with chromium. It involves dipping the metal in solutions containing chromic acid or sulfuric acid.
Examples
Some examples of chrome plating metal finishes include automotive bumpers, electronic hardware, and plumbing fixtures.
19. Gold Plating Metal Finishes
A process in which a layer of gold is applied to the base metal through an electroplating process. It involves dipping the product into a solution containing gold and cyanide or other solutions that contain various additives and electrolytes.
Examples
Some examples of gold plating metal finishes include jewelry, commemorative coins, and dental alloys.
20. Silver Plating Metal Finishes
A process in which a layer of silver is applied to the base metal through an electroplating process. It involves dipping the product into a solution containing silver and cyanide or other solutions that contain various additives and electrolytes.
Examples
Some examples of silver-plating metal finishes include jewelry, electronic connectors, and medical alloys.
21. Plasma Etching Of Metals
A metal finishing process uses a plasma torch to remove the top layer of the surface of a metal. This technique can be used to create decorative or custom-designed finishes, parts with an uneven finish, and other various functions.
Examples
Some examples of plasma etching include metal components with a matte or satin finish, parts that need to resist corrosion, and car bumpers.
22. Tin Plating Metal Finishes
A type of electroplating process that coats base metal with a layer of tin. It involves dipping the product into a solution containing stannous chloride or other solutions that contain various additives and electrolytes.
Examples
Some examples of tin plating metal finishes include architectural, consumer, and industrial applications.
23. Buffing Of Metals
A metal finishing process that uses a buffing wheel to move the surface of a metal in several directions. Buffing can be used to apply different finishes, depending on the speed of the machine and whether it is moving towards or away from the part being polished.
Examples
Some examples of buffing include metal components with a mirror finish, parts that need to resist corrosion, and metal surfaces with a bright or satin finish.
24. Abrasive Blasting Of Metals
A process that uses fine or coarse-grained materials to roughen the surface of a product to create better adhesion for paint, powder coatings, and other types of finishes. It involves using any mechanical action to wear away at the material surface.
Examples
Some examples of abrasive blasting metal finishes include automotive primer, decorative paint, and powder coating.
25. Coarse Grinding Of Metals
A process that uses rotating discs with diamond crystals attached to them to remove excess material from a part.
Examples
Some examples of coarse grinding metal finishes include removing excess weld material, polishing, and prepping for welding.
26. Fine Grinding Of Metals
A process that uses rotating discs with silicon carbide crystals attached to them to remove excess material from a part.
Examples
Some examples of fine grinding metal finishes include polishing and prepping for paint.
27. Honing Of Metals
A process that uses abrasive stones to remove burrs or produce a smooth finish on the edges of a metal part.
Examples
Some examples of honing metal finishes include removing sharp edges, removing machine marks, and polishing.
28. Sanitizing Of Metals
A metal finishing process that uses fine-grit sandpaper to remove a fraction of the metal from the surface. This creates a rough finish to improve corrosion resistance and create a matte appearance.
Examples
Some examples of satanizing include metal surfaces with an uneven finish, parts that need to resist corrosion, and metal components made out of low-cost materials.
29. Lapping Of Metals
A process that uses flat stones to produce a smooth finish on the surface of an object. It involves using any mechanical action to wear away at the material surface.
Examples
Some examples of lapping metal finishes include removing excess weld material, polishing, and prepping for welding.
30.Sandblasting Of Metals
A process that uses compressed air to propel sand or another abrasive material against the surface of an object.
Examples
Some examples of sandblasting metal finishes include automotive primer, decorative paint, and powder coating.
31. Wrought Iron Finishes/Metal Finishes
Wrought iron is a lightweight metal alloy made from smelting iron ore in a furnace with limited oxygen. The advantage of using this method over other types of casting and melting processes is the material’s increased malleability and ductility.
Examples
Some examples of wrought iron metal finishes include automotive trim and fencing.
32. Tumbling Of Metal Finishes
A process that uses a rotating drum filled with small media to remove burrs form, texture, or polish the surfaces of metal parts. It is typically used as a polishing step before plating or painting for metal parts but can also be used before welding for prepping.
Examples
Some examples of tumbling metal finishes include removing excess weld material, polishing, and prepping for welding.
33. Electroforming Metal Finishes
A process that uses electricity to deposit metal onto an object. It is typically used for coating objects with thin layers of metal but can also be used to produce complex shapes that are difficult or impossible to cast in one piece.
Examples
Some examples of electroforming metal finishes include electrical components and decorative pieces.
34. Sputtering Metal Finishes
A coating deposition process that uses an ionized gas (typically argon) to release atoms onto a surface, which then form a solid film after they combine with the substrate. Sputtering is also known as ion plating.
Examples
Some examples of sputtering metal finishes include automotive trim and fencing.
35. Shot Peening Of Metals
A metal finishing process that uses a blast of small steel balls to compress the surface of a metal. This compresses the material and makes it more resistant to wear, thereby increasing its lifespan.
Examples
Some examples of shot peening include metal components with an uneven finish, car bumpers, and parts that need to resist corrosion.
36. Chromate Conversion Coating Of Metals & Alloys
A chemical conversion coating process that uses chromate compounds to coat steel. The chromates react with the surface of the metal part, creating a highly corrosion-resistant layer.
Examples
Some examples of chromate conversion coating include iron and steel fasteners.
37. Zinc Plating Metal Finishes
A process that uses a chemical bath to deposit a layer of zinc on the surface of a metal part. Zinc plating is the most common method for protecting steel and iron from corrosion, and it also improves the metal’s ability to conduct electricity and form smooth surfaces.
Examples
Some examples of zinc plating include iron and steel fasteners, screws, and bolts.
38. Cadmium Plating Of Metals
A metal finishing process that uses cadmium as a coating for components made from steel, copper, and other metals to form a thin, decorative, and protective layer of cadmium oxide on the surface of the metal. The thickness of this layer helps protect the underlying metal from rust, wear, and corrosion.
Examples
Some examples of cadmium plating include decorative metal surfaces, metals with a low-gloss finish, and corrosion-resistant components.
39. Non-Chromium Plating Of Steel And Iron For Industrial Use
A process that deposits a layer of zinc, copper, nickel, or cadmium on the surface of steel and iron to improve corrosion resistance. Aluminum can also be used as a non-chromium coating for steel to increase the metal’s resistance to saltwater corrosion.
Examples
Some examples of non-chromium plating include steel parts and engines.
40. Non-Chromium Plating Of Iron And Steel For Galvanic Protection
Galvanic protection uses the natural process of dissimilar metal reactions to protect a metal surface from corrosion. It works by attaching different metals (that have very different electrode potentials), which creates an electrical path between them that prevents corrosion.
Examples
Some examples of non-chromium plating for galvanic protection include fasteners made with zinc or cadmium coating.
41. Non-Chromium Plating Of Iron And Steel For Decorative Use
A process that deposits a layer of zinc, copper, nickel, or cadmium on the surface of steel and iron to improve corrosion resistance. Aluminum can also be used as a non-chromium coating for steel to increase the metal’s resistance to saltwater corrosion.
Examples
Some examples of non-chromium plating for decorative use include steel parts and engines.
42.Passivation Of Metals
The chemical process of removing free iron from a metal’s surface so it won’t rust. Passivation also reduces corrosion, decreases the metal’s electrical conductivity, increases the metal’s hardness, and improves the part’s appearance.
Examples
Some examples of passivation include cleaning parts before painting, making the aluminum more resistant to saltwater corrosion, protecting iron from rusting, and improving the look of zirconium by removing its red oxide color.
43.H2SO4 Passivation Of Zinc (Hot-Dip) Plated Cr20C Armco Iron
A chemical bath that uses a strong acid to remove rust, scale, and other paint or coating from metal parts so they can be painted with an etching primer. The acid dissolves the oxide layer on the surface of the metal and makes paint adhere better.
Examples
Some examples of an acid bath include a chemical dip to remove paint from metal parts, a process that removes rust and scale on steel products, or a treatment that removes old coatings from stainless steel.
44. Black Oxide Coating Metal Finishes
A process that produces a layer of magnetite (black iron oxide) on the surface of metal parts to make them more rust and corrosion-resistant. Black oxide is also used for decorative effects, such as making steel look like cast iron.
Examples
Some examples of black oxide coating include using a chemical bath to add a protective or decorative finish on metal products, making stainless steel look like cast iron, and protecting iron from rusting.
45. Oil And Grease Resistant Rubber Overlay On Metals
A process in which a thin layer of rubber is applied to a metal surface. The rubber provides oil and grease resistance by creating a chemical bond with the substrate. Rubber overlays are often used on mechanical equipment instead of painting, which can be exposed to oils.
Examples
Some examples of a rubber overlay include protecting metal surfaces from corrosion, making steel look like cast iron, and coating metal parts so they can be used in food or pharmaceutical applications.
46. Alkaline Decomposition Treatment Of Metals To Minimize Corrosion
The process of treating metal products with an alkaline solution to change their surface chemistry and improve corrosion resistance. This process changes the coating’s chemical composition, which enhances its performance in certain conditions.
Examples
Some examples of alkaline decomposition include a process that reduces or eliminates rust on steel parts and a technique that makes stainless steel more corrosion resistant.
47. Aluminum Alloy Protective Film-Passivation Treatments
A thin layer of aluminum oxide that’s deposited on the surface of an aluminum alloy to increase its resistance to corrosive chemicals, such as seawater or fertilizer. This coating also reduces friction and reduces the material’s susceptibility to exfoliation corrosion.
Examples
Some examples of the protective film include making the aluminum more resistant to saltwater corrosion, coating metal parts with an atomized mist of molten metal, and protecting steel surfaces from rusting.
48. Acid Etching Of Metals
A metal finishing process that uses a chemical solution or abrasive paste to remove the top layer of the surface of a metal. This technique is used to create a matte appearance, remove rust or expose an underlayer.
Examples
Some examples of acid etching include metal surfaces with an uneven finish, parts that need to resist corrosion, and metal components made out of low-cost materials.
49. Electroless Nickel Plating Metal Finishes
A corrosion-resistant coating that contains a layer of nickel, rather than metal with a higher melting point. Electroless nickel plating is typically used to improve lubricity and for decorative or functional purposes.
Examples
Some examples of electroless nickel plating include adding a decorative or functional finish to metal parts, protecting steel from rusting, and adding lubricity to metal surfaces.
50. Metal Spraying By Gas Metal Arc Welding
A metal finishing process that uses an electric arc between a consumable wire electrode and the part being welded. Gas metal arc welding is often done using a gas shield and can be used to join several materials together.
Examples
Some examples of gas metal arc welding include metal components with a bright finish, parts that need to resist corrosion, and structures for industries such as aerospace, automotive and heavy equipment.
51. Pickling Of Metals
A cleaning process that uses a chemical to remove rust, scale, and other undesirable materials from ferrous metals. The metal is then rinsed with water or a neutralizing solution to remove the chemicals used during pickling.
Examples
Some examples of pickling include removing rust, scale, and other undesirable materials from metal parts, removing the effects of corrosive chemicals on metal surfaces, and making steel more resistant to rusting.
52. Soldering Fluxes For Copper Alloys
A process that joins metal parts by melting them together. Soldering requires tools and supplies, such as solder (a metal with a low melting point) and flux (a cleaning agent to remove oxidation).
Examples
Some examples of soldering include joining metal parts and joining copper components.
53. Wrought Carbon Steels
Carbon-containing alloys are typically used for their functional properties rather than their aesthetic qualities. These alloys are usually used for mechanical applications rather than decorative purposes.
Examples
Some examples of wrought carbon steels include parts that resist corrosion, components with high strength, and metal surfaces with a low-sheen finish.
54. Aluminum Alloys
Mixtures of aluminum and other metals improve the mechanical properties, such as strength and corrosion resistance, while also lowering the weight of the alloy compared to pure aluminum. These alloys vary in terms of composition and the properties they offer.
Examples
Some examples of aluminum alloys include strong metal components, corrosion-resistant parts, and lightweight materials.
55. Stainless Steels
A group of metals that contain a minimum of 10.5 percent chromium and often nickel and molybdenum as well. These components form an invisible oxide layer on the metal surface, which is more resistant to corrosion than other metals.
Examples
Some examples of stainless steel include high-performance parts, metal surfaces that are harder than steel, and heat sinks.
56. Lead-Bismuth (Pb-Bi) Alloys
Alloys of lead (Pb) and bismuth (Bi), with or without other metals, have a low melting point. These alloys are typically brittle and used for creating bearings in hard-to-reach locations.
Examples
Some examples of lead-bismuth (Pb-Bi) alloys include metal components used in hard-to-reach areas, parts that require low friction, and strong bearings.
57. Chrome Plating Or Chromium (Cr) Plating Of Metals
A metal finishing process that uses chromium to form a thin, decorative, and protective layer of chromium oxide on the surface of a metal. The thickness of this layer helps protect the underlying metal from rust, wear, and corrosion.
Examples
Some examples of chrome plating include surfaces that are harder than stainless steel, corrosion-resistant metal structures, and parts with a shiny or matte finish.
58. Cold-Dip Galvanizing Of Metals
A process that coats metal parts with zinc (Zn) after immersing them in a bath of molten zinc. Cold-dip galvanizing protects the underlying metal from rust and corrosion, which makes it useful for outdoor applications.
Examples
Some examples of cold-dip galvanizing include outdoor metal structures, components that need to resist corrosion, and spraying metal surfaces with zinc.
59. Physical Vapor Deposition (PVD)
A process that coats metal objects with a thin, decorative, and protective layer of metal atoms using thermal evaporation or other vaporization techniques. The thickness of this layer helps protect the underlying metal from rust, wear, and corrosion.
Examples
Some examples of physical vapor deposition include decorative metal surfaces, metals with a low-gloss finish, and corrosion-resistant components.
60. Phosphate Coatings For Steel
A thin, decorative coating consisting of zinc phosphate that forms on the surface of a metal after immersing it in an acidic or alkaline solution containing hydrogen phosphate to create the phosphoric acid by-product.
This process is typically used as a low-cost alternative to painting and other forms of corrosion protection.
Examples
Some examples of phosphate coatings include metal structures that resist corrosion, car bumpers, outdoor metal structures, and surfaces that have a matte or satin finish.
Types Of Metal Finishes – Conclusion
As you can see, many different types of metal finishes range from decorative to corrosion-resistant. The use of metal finishes is a choice, not an obligation. However, understanding the different types of metal finishes may help you decide which finish using on your metal components.
Other factors that may affect your choice of metal finishes include the need for a shiny or matte finish, corrosion-resistant properties, and how you plan to use the finished product.